Routine Maintenance
The Department maintains a Routine Schedule of Activities (shown below) as a part of it's ongoing maintenance program. It is estimated that 90% of the cost to overlay asphalt roads can be saved by extending the existing life of the pavement by doing only routine maintenance. By prolonging the existing life of asphalt pavements by eliminating routine asphalt overlays will provide needed dollars and will not hinder the mission. This Department does not maintain private roadways or drives. The Department maintains a current Sediment Control Plan (approved by the Soil Conservation District) for highway maintenance, rehabilitation, overlays and drainage improvements for routine work performed without the use of construction drawings. View a brief history of the Development of our Roadways since 1639.
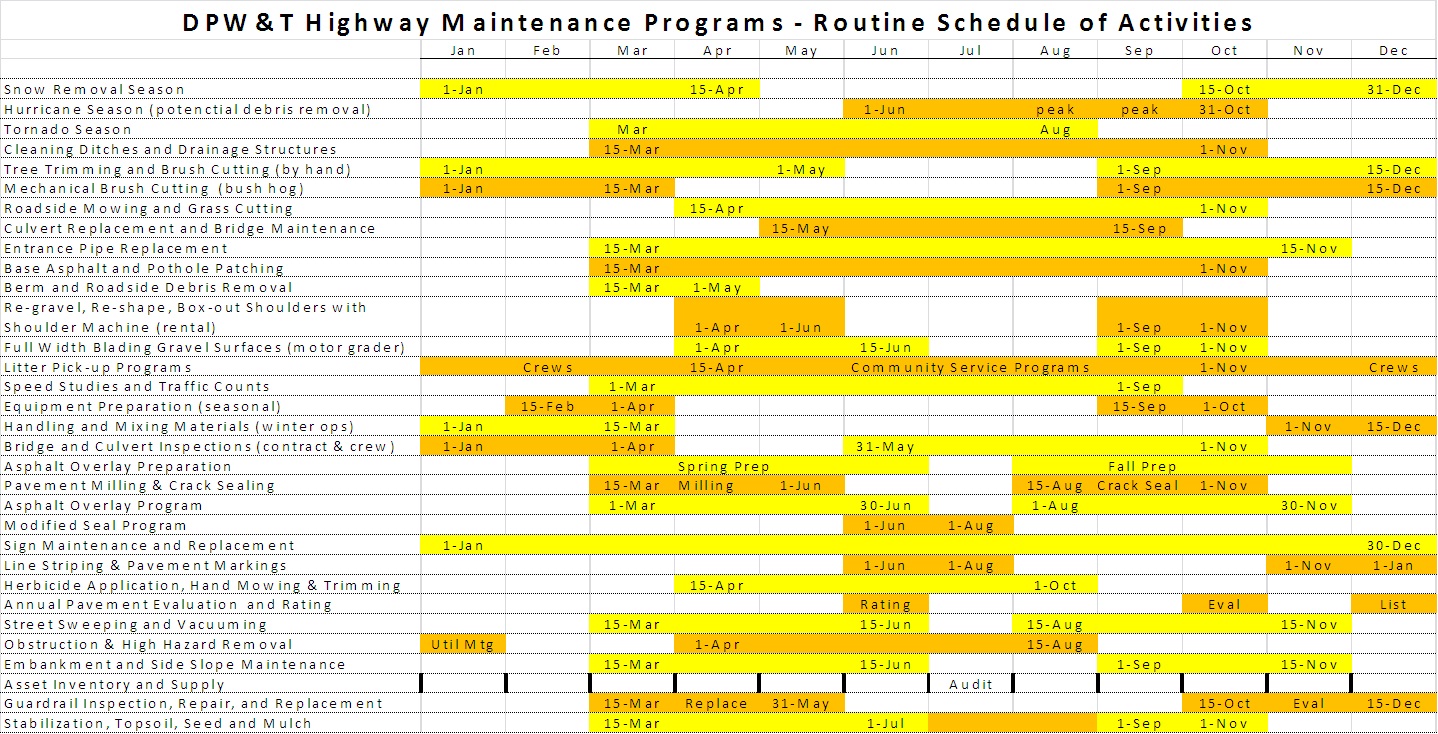
To report issues along or on State Highways (ie. MD 234, MD 246, MD 235, etc.) Click Here
Maintenance Requests
If a County road is damaged, a sign is down/missing and/or there is an apparent need for maintenance or repair (i.e. pothole, drainage ditch, etc.) contact the County Highways Division at (301) 475-4200, fax information to (301) 863-8810 or fill out our Maintenance Request Form
Sediment Control Plan
The County maintains a Sediment Control Plan for highway maintenance, highway rehabilitation, asphalt overlay and drainage improvements for which construction plans and drawings are not required and do not involve work within blue-line streams, wetlands and their respective buffers. The work for this type of construction is confined to twenty five (25) feet from the centerline of existing roadways or to the limit of St. Mary's County right-of-way, whichever is greater. Work allowable under the Plan includes, but is not limited to; clearing and grubbing, sediment control, stabilization, outfall protection, drainage ditch and culvert maintenance, excavation and filling and placement of shoulder material.
Drainage Ditches
Approximately 65 miles of ditch-work is performed by highway maintenance crews annually using gradall machines. Roadway ditches are provided for the controlled removal of surface water from the right-of-way. Various ditch lining materials are used to prevent erosion in conditions with steep slopes, high velocity flows and poor soil conditions. It is recommended that roadside ditches be cleaned on a minimum eight (8) year cycle and following major storm events. The County uses different types of linings to help stabilize it’s roadside ditches; flexible ditch linings such as grass, vegetative mixes, geo-textile filter fabrics, un-grouted rip-rap and, in extreme conditions, rigid linings like Portland cement, bituminous concrete and grouted rip-rap. The maintenance of ditches along roadways that traverse wetlands, if the work involves re-cutting to design dimensions is covered under the County’s Regional Letter of Authorization as a State permitted activity. Our goal is to limit the number of flooding incidents by keeping drainage-ways clear with regular maintenance and cleaning.
Shoulder Maintenance
A shoulder is the portion of the roadway adjacent/contiguous with the paved travel-way and may be composed of gravel, crushed rock, bituminous, surface treatment, or grass on native soil. An integral part of the DPW&T maintenance program is the inspection and repair (surface treating, cutting, shaping, re-compacting, adding new gravel) of roadside shoulders. This activity is typically performed twice a year; between April 1st to July 1st and September 1st to November 1st. Well designed and properly maintained shoulders are also extremely advantageous and necessary on rural roads because they: essentially serve as structural lateral support for the roadway surfacing; provide space for the occasional motorist who needs to stop for mechanical reasons; provide lateral clearance for signs and guardrails; allow space for oversized farm vehicles, pedestrians, bicyclists and mail vehicles use; help to discharge drainage away from pavement to minimize pavement breakup; ease performance of maintenance operations such as snow removal; and can improve sight distance. For this reason, shoulders on low volume roads are often constructed of gravel.
Accidents are likely to occur where drivers are called on to make decisions under circumstances where their vehicles are unable to respond properly. When a vehicle leaves the roadway, the driver no longer has the ability to fully control the vehicle. Maintaining useable shoulders along rural roads helps to provide a clear recovery and maneuver room ("space") to escape potential accidents or reduce their severity. The two (2) basic maintenance problems we face are: shoulder "drop-offs" which should be scheduled for maintenance and immediate repair if the "drop" from the edge of pavement is greater than 2 inches; and shoulder "build-up" which is handled by cleaning the shoulders, especially after the winter season, and berm removal operations prior to paving.
Embankments and Side-Slopes
There are numerous maintenance requirements associated with the stabilization of roadway embankments and side-slopes including repair to cut or fill slopes due to surface erosion, slope sluffing and embankment settlement. Oftentimes, these types of problems do not become evident until after new roadways are constructed and accepted by the County. Once an area of concern has been identified remedial actions are much more costly which may include the flattening of slopes or the installation of slope drains, topsoil seed and mulch.
Drainage Structures
Over 800 maintenance requests from residents are processed annually. It is estimated that 80% of this effort is drainage related. For typical drainage related questions and answers. Approximately 3,000 linear feet of deteriorated metal cross pipes are replaced by our Highway maintenance crews each year. Inlets require continual maintenance attention due to clogging with leaves, underbrush, sediment, debris and even ice. If not unplugged immediately, the resulting water ponding can create a traffic hazard on the roadway, soft ground conditions beneath the pavement or wet conditions within yards on private property. Water infiltration into the sub-grade can create a myriad of structural problems/failures within the pavement surface. Where maintenance easements do not exist, adequate access and necessary equipment working room has to be secured from the land owner.
Pavement and Bridge Repairs
Failure and subsequent repair of roadway pavement constitutes a large percentage of highway maintenance expenditures. These structural problems including concrete pavement spalling, faulting, pumping, blowups and asphalt pavement cracking, raveling and rutting are easily recognized. Many of the corrective procedures such as crack sealing, pavement milling, pothole patching, berm removal, wedge-and-leveling operations are performed as part of our annual Overlay Preparation procedures. In addition, in order to provide proper pavement subsurface drainage we often have to raise the roadway grade line above the water table, lower the water table by means of deep side ditches, install free draining and day-lighted base material and perforated under-drain pipes. As a follow-up to our bridge inspection program, a listing of direct and indirect maintenance recommendations is prepared and forwarded to the Count Highways Division for action. Deck joints, approaches, wearing surface, railings, abutments and piers, painted surfaces
Potholes and Sinkholes
Potholes form when moisture collects in small holes and cracks in the road surface. As temperatures rise and fall, the moisture expands and contracts due to freezing and thawing. This breaks up the pavement and, combined with the weight of passing cars, eventually results in the formation of potholes. Depending on the amounts of snow, salting and plowing required, the number and size of potholes will vary considerably. The AAA offers the following advice to protect your vehicles from pothole damage:
Look ahead. Make a point of scanning the road ahead for potholes. If you see a pothole in advance, you might have time to avoid it, so it’s important to stay focused on the road and not on any distractions inside or outside of the vehicle. Before swerving to miss a pothole, check surrounding traffic to make sure you will not cause a collision or endanger nearby pedestrians or cyclists.
Slow down. If you can’t avoid a pothole, reduce speed safely and be sure to check the rearview mirror before any abrupt braking. Hitting a pothole at higher speeds greatly increases the chance of damage to tires, wheels and suspension components.
Beware of puddles. A puddle of water can disguise a deep pothole. Use care when driving through puddles and treat them as though they may be hiding potholes.
It is the goal of the Highway Maintenance Division to maintain County streets in good repair, including repair of potholes and sinkholes. Once County Roads Maintenance staff are notified of a pothole, a crew is dispatched to repair the defect. St. Mary's County roadway crews primarily uses an asphalt emulsion cold mix or the square cut patch method to repair potholes, depending on the size and condition of the roadway. For small to medium sized potholes, crews fill the void with water based mixing grade asphalt emulsion. This method is both environmentally and economically friendly and effective in repairing these types of roadway defects. For larger sized potholes, square cut patching may be required to effectively correct the problem. This requires grinding or cutting out a portion of the roadway surrounding the pothole, repairing the sub-base material and patching the roadway surface. A less commonly used method of pothole repair includes the use of asphalt concrete. During the winter months ,even though Public Works may fill a pothole, the water underneath can freeze up that night and push the "cold patch" right back out again. This is just a condition of the winter storm season and cold temperatures.
Report it. Save yourself and others from hitting the same pothole again and again by reporting it to us at (301) 475-4200 or on-line. For more information on potholes and sinkholes, click here.
Sidewalks
The County Highways Division keeps a list of sidewalk problem locations that have been reported by residents. If the sidewalk is settled, but not broken, the sidewalk will be temporarily patched with asphalt if there is a tripping hazard.
Topsoil, Seed and Mulch
Typically, excess clean fill dirt and topsoil is stockpiled at the St. Andrews landfill facility from independent loads brought in for disposal by residents, contractors and County crews. A rental tub grinder is utilized to produce a mulch product from wood and yard waste debris (branches, limbs, leaves, pallets) and stockpiles the material. Some of the product is used as a field dressing for maintenance of roadside ditches and for landscaping around County-maintained buildings, but the majority is returned to our residents at no charge. Otherwise, fiber mulch is purchased in fifty-pound bales at a cost of approximately $2.75 per bale. It is estimated that the annual usage for grass seed is between 5,000 and 10,000 pounds. Bid prices range between $1.15 per pound for SHA-1 mixture. $0.90 per pound for Common Perennial Rye Grass, $0.85 per pound for Kentucky 31 and $0.40 per pound for SHA Temporary Mixture. Items associated with these stabilization operations such as erosion control matting, silt fence and galvanized staples are also purchased under Blanket Purchase Agreement(s).
Maintenance Priorities
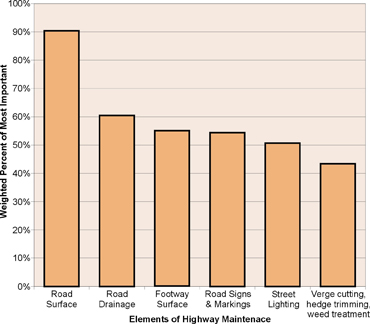
Please call 911 for dangerous roadway or pedestrian emergencies such as: Dangerous obstructions in roadways (debris, trees or large animal carcasses) Downed utility lines such as electric and phone Accidents Roadway(s) flooding Snow and ice conditions Hazmat spills (ie. gasoline, oil, etc. ) Traffic or pedestrian signal malfunction Traffic control (stop and speed limit, etc.) signs missing or damaged
High Priorities
During normal working hours, please call (301) 475-4200 or fill out our Maintenance Request Form. After normal working hours or on weekends, please telephone Public Safety at (301) 475-8016. Communications dispatchers will then call out repair crews for high priority items.
Traffic visibility problems resulting from trees or shrubs blocking the view of oncoming traffic Missing stop signs, speed limit signs and advisory signage Sinkholes, damaged pavement markings/striping/stop bars Animal carcass removal obstructing travel lanes Flooding in roadside ditches or in/across roadways Debris removal after severe weather events and snow removal
Medium & Routine Priorities
Normal priority items can be phoned in to (301) 475-4200, faxed to (301) 863-8810, e-mailed to our Highway Maintenance Division Manager or simply fill out our Maintenance Request Form.
- Pothole and guardrail repairs
- Pavement surface maintenance
- Sidewalk and shoulder damage
- Street sweeping and vacuuming
- Removal of non-dangerous items from roadways or rights-of-way
- Damaged curb, drainage structures, driveway pipes and culverts
- Tree limbs overhanging streets or sidewalks
- Mowing, tree trimming, cutting grass in median islands
- Ditch drainage and embankment erosion (not flooding)
- Litter pickup and graffiti (non-offensive) removal
- Repair of missing or damaged street names signs or other informational signs (not traffic control signs)
- Reports of street light problems (not traffic signal malfunctions)
To report issues along or on State Highways (ie. MD 234, MD 246, MD 235, etc.) use https://mdotsha.my.salesforce-sites.com/customercare/request_for_service